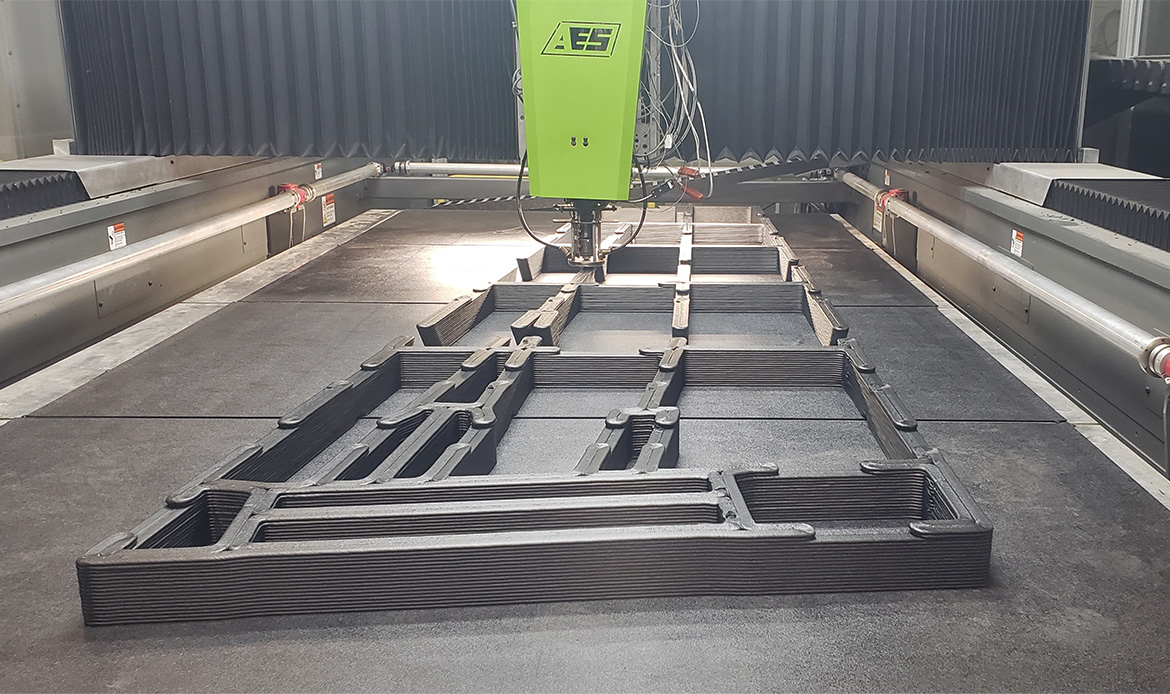
What is Large Format Additive Manufacturing?
Large Format Additive Manufacturing, or more commonly known in the industry as LFAM, is a large output, extrusion deposition 3D printing technology. Similar to FDM or conventional desktop style 3D printers that use filament, LFAM is on an industrial scale in both terms of rated output and physical print volume. The most common type of material used in this setup are thermoplastic composites in the form of pellets similar to those used in injection molding.
The first LFAM 3D printer was developed back in 2015 in a partnership between Oak Ridge National Lab’s MDF department and machine tool builder, Cincinnati Inc. Big Area Additive Manufacturing or BAAM as the printer was called made its claim to fame when it 3D printed a car at the 2015 IMTS show in Chicago. Today, there are many machine options available to choose from when it comes to buying large format printers; BAAM, LSAM, MasterPrint, etc.
LFAM’s clear advantage is the speed at which it can deposit material, sometimes measured at over 100lbs /hr and the physical size in which it can make parts, usually measured in feet and on really large machines tens of feet in size!
LFAM 3D Printing Highlights
Major benefits stemming from LFAM solutions is largely dependent on geometry. The rule of thumb is, if it’s easy to make something through conventional manufacturing methods, you are likely not going to see a large benefit from using LFAM; however, when you are dealing with large and complex shapes with curvature and deep projections, LFAM can show tremendous value.
Benefits of Large Format Additive Manufacturing
Speed is the number one value proposition when it comes to most LFAM solutions.
- • 10ft+ sized tools and parts that can weight 1,500 lbs can be printed in ONE DAY within a 1/4″ of the final dimension.
- • Near-net printing results in little material removal needed; faster throughput in the CNC department.
- • Part consolidation in assemblies and structures
With the right geometries, LFAM solutions can easily be up to 40% cheaper.
- • Near-net printing results in an incredibly small amount of material waste. Conventional tool making processes can waste up to 75% of the material bought and paid for!
- • Thermoplastics can be more economically priced in some situations when compared to metallics.
- • Thermoplastics can be more durable than wood and foam; resulting in a lower overall amortized piece price in the precast industry.
- • Skip tooling and molds altogether and print your parts directly with thermoplastic composites.
- • Part consolidation when it comes to assemblies and structures.
3D printed thermoplastic composites is a new material type being offered that can help fill in the gaps where something like a metal is overkill, but a high dense foam is not durable enough.
- Tailor the material to the specific job durability needs; does a mill fixture really need to be made from a metallic material?
Partnership with CEAD Group
In late 2023, AES entered into a Collaborative Partnership with CEAD Group (Netherlands) and acquired a CEAD Flexbot Robotic 3D Printer. See the full details of the press release here.
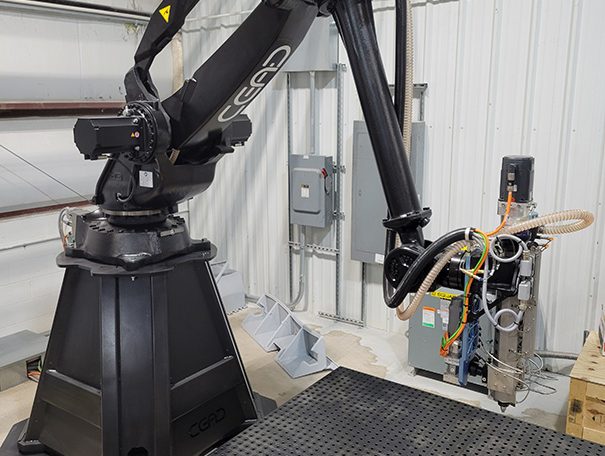